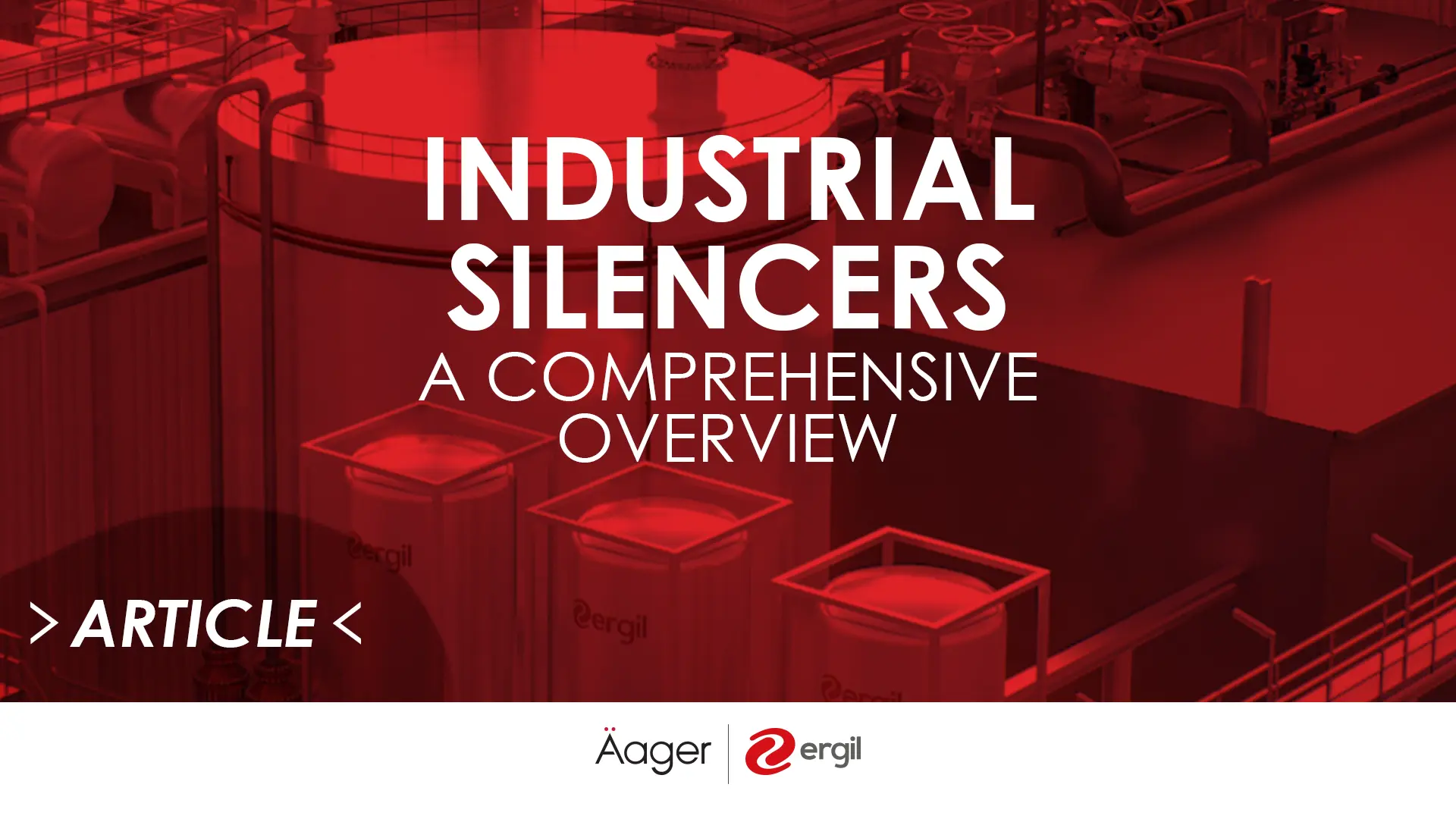
Industrial Silencers: A Comprehensive Overview
Quite all industrial equipment and devices generate some noise, usually well above the allowed limits. Those limits are different in the various countries: in Europe was stated as 87 dB(A) from the European commission, even if the limits are different in the single European countries, mainly as 85 dB(A), but with an idea to lower it.
In the U. S. A. the limit was fixed by the NIOSH at 85 dB(A) during the 8 working hours, and 50 dB(A) during the night.
Therefore, it will be necessary to provide something to respect those limits.
That could be reached by using static noise reduction devices, Acoustical Enclosure, not included in our scope and dynamic noise reduction devices, i.e. silencers, devices to be put online to reduce the streams noise, which is traveling along the pipes.
In industrial settings, silencers are crucial components used to moderate and control noise levels, ensuring a conducive working environment and complying with noise pollution regulations. These silencers are categorized into three main types: absorptive, reactive, and expansion (and even a combination of two types, mainly reactive plus a second absorptive type section or expansion plus a second absorptive type section). Each type has its unique set of applications, structures, and mechanisms for noise reduction.
Absorptive Silencers
Absorptive silencers are predominantly utilized when noise is fairly distributed across all octave bands. These silencers can achieve a maximum noise reduction of up to 55 dB in every octave band. If They are to be used in scenarios where very low noise is required, typically around 40-50 dB(A), it is imperative to meticulously monitor the noise self-generated by the splitter panels silencers.
Applications and Specifications
The primary applications for absorptive splitter panels silencers include the suction and exhaust of gas turbines and boiler discharge, especially in power plants. When used for gas turbine suction, the silencers must be constructed from AISI 304 and fabricated in a distinct, clean shop section to avoid contamination by carbon steel.
Special attention is required for exhaust silencers due to the elevated discharge temperatures and the resulting thermal expansion. It is critical to allow the perforated sheets to expand freely to circumvent thermal stresses. If the silencer is positioned within the chimney, post the diverter, it should be placed at least 1.5 DIA. away from the diverter outlet, to avoid the photoabsorbent material to be blown away.
These silencers could be cylindrical section or square/rectangular section
Absorptive silencers can feature either parallel splitter panels or concentric splitter panels, with the former being the more cost-effective manufacturing option. The absorption materials used are pivotal, with a recommendation for basaltic wool with a density of 100 Kg/m³, shielded by a substantial fiberglass cloth with a ¼" thickness. The material on the shell can have a density of just 80 Kg/m³. The external protection of these material will be perforated sheets, designed with appropriate holes diameter, pitch, and open area.
Design and Efficiency
Absorptive silencers are meticulously designed to meet specific requirements, ensuring optimal performance. The dynamic insertion loss is in accordance with the outlined specifications and has been field-tested on silencers that have been manufactured and supplied to some customers. The absorption package is created in "pillows," fully sealed to prevent materials from being blown out, and are typically 1m by 1m to align with the perforated sheets dimensions.
Vent Silencers
When you vent a gas or a steam to atmosphere, it occurs a lamination effect, so that the upstream gas pressure will go to the atmospheric pressure and the temperature will remain the same, except for CO2, which temperature will be 20 degree C lower than the upstream temperature. The steam vent will follow the same process (lamination), but in accordance with Mollier diagram, which will give the downstream temperature of the steam
Vent silencers are a combination of expansion and absorptive silencers, specifically designed to minimize noise created by the venting of high-pressure steam, air, or gas to the atmosphere. These silencers are integral in various industrial applications, helping in mitigating the noise generated during venting processes and steam blowing to clean the pipes before using them.
Design and Efficiency
The vent noise level is calculated from NASA studies and Lightnill formula, in addition to several field measurements during gas and steam venting.
The vent silencers are usually cylindrical, but could be with square/rectangular section to allow several streams venting in the same silencer, to save cost in manufacturing.
Special attention is required for vent silencers due to the elevated discharge temperatures and the resulting thermal expansion. It is critical to allow the diffusers set and the shell and splitter panels perforated sheets to expand freely to circumvent thermal stresses. Silencers could be equipped with a special axial expansion joint at their inlet to avoid thermal stressed due to constricted expansions. At their inlet there is a pack of expansion diffusers (could be from 1 to 6), which job is to move the low frequency noise to high frequency noise, which is easier to be broken down by the second stage splitter panels silencer (quite always we have a second stage with splitter panels; only with some low-pressure vent and not stringent noise requirements we may have only the first stage with diffusers). The best suggested number of diffusers is 3 to 4. Take note that this kind of silencer will have important pressure drop; usually Customers allow a 20% pressure drop on the set upstream pressure of the vent valve. The diffusers DIL is based and was field tested on check silencers made for this purpose. With these types of silencers, it is possible to reach even 60-70 Dynamic insertion loss, even it is suggested to no go up more than 55-60 dB
The silencer could be equipped too with a rain hood with discharge to the top to avoid noise reflection downstairs.
The diffusers materials will be AISI 304 or better, while the silencer body will be normally made by carbon steel.
Take note that the vent silencers are NOT pressure silencers subjected to codes.
A category apart are the blowing silencers, used to clean the steam pipe line before there operation; the principle is still the same, with the difference that the inlet will be radial with a pot just in front of the inlet to receive the eventual garbage inside the vented pipes (stones, hats, gloves, screw, nuts, pliers and so on) left by the workers during their job.
Reactive Silencers
Reactive silencers, another variant, use a different mechanism to control noise. They are designed to reflect the sound waves, leading to the interference and subsequent cancellation of the noise. Reactive silencers are particularly effective in dealing with low-frequency noises and are vital in industrial settings with predominance of such noise levels.
They may have too a second stage absorptive type silencers, made by standard cylindrical silencers (with or without central plug) or splitter panels silencers.
The first silencer section (the reactive part) could be single stage (two chambers) or double stage (three chambers). this one not suggested because the DIL increasing will be more expensive than adding a second absorptive type. The choke tubes (connecting pipes between the two silencer chambers) could be profiled for lower pressure drop or just straight cut for higher pressure drop. These tubes could be selected to have the required low frequency and high frequency cut off.
These silencers are normally manufactured by carbon steel.
The reactive silencer is named “pi-filter” and was calculated with NACA formulas, Bolt Beranek and Neumann studies and know-how of important Noise Companies in the world.
Our reactive silencers could also calculate the D.I.L. for the rupture disc and the possible heat exchanger located downstream the silencer. The D.I.L. of our reactive silencers were tested on hundreds of supplied silencers
Application and Implementation
Reactive silencers are adaptable and can be implemented in some industrial applications to manage and mitigate low-frequency noise effectively. They play a crucial role in maintaining the acoustic environment within permissible levels, ensuring compliance with industrial noise regulations and standards. Main applications are for big yachts, internal combustion engines and gensets.
Conclusion
Industrial silencers are indispensable components in the industrial sector, aiding in the management and reduction of noise levels. Whether it is the absorptive silencers used in gas turbines and boiler discharges in the energy plants, vent silencers managing high-pressure releases in energy plants, compressors vent in storage and compression station for natural gas or reactive silencers dealing with low-frequency noises installed aboard of Mega-yachts, big cruising ships or military services boats, each type serves a specific purpose in maintaining a balanced acoustic environment. The meticulous design, material selection, and application-specific customization are crucial in ensuring the optimal performance and efficacy of these silencers in various industrial settings.
Rev.1 October 5.st, 2023
Rev.0 September 29th, 2023
Roberto Mozzatto
Technical Advisor