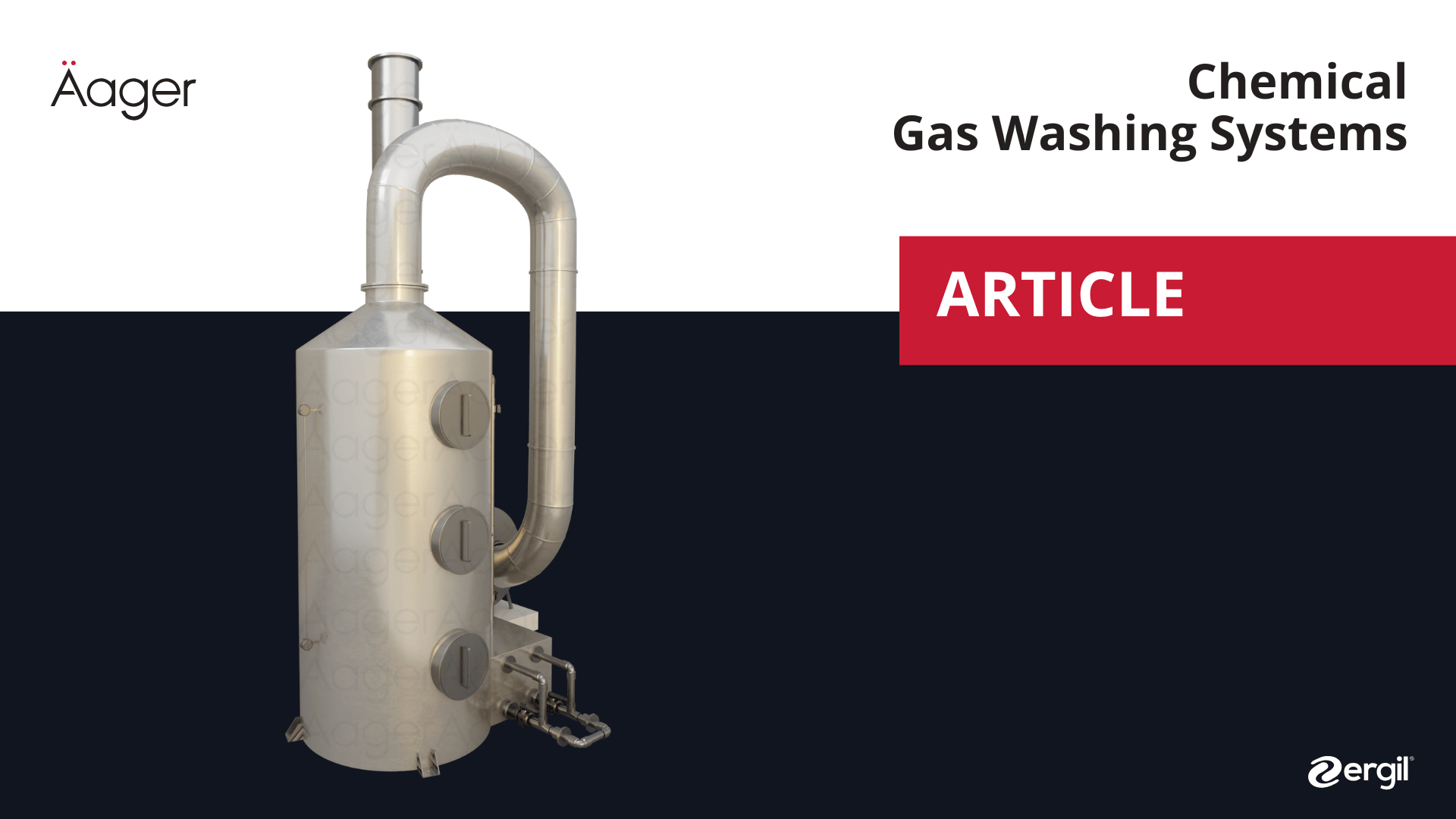
Chemical Gas Washing Systems (Scrubber)
Industrial activities generate harmful gases and odors that pose serious risks to human health and the environment. To mitigate these effects, industries employ gas purification systems, commonly known as scrubbers. These systems are designed to remove or neutralize pollutants from exhaust gases before they are released into the atmosphere.
Working Principle of Scrubbers
Scrubbers operate on the principle of gas absorption in liquids. The primary function of a scrubber is to capture waste gases and pass them through a washing process, where they interact with a liquid medium (often water or a chemical solution). The gas is drawn from the environment using a suction fan and is forced upward through a bed of packing materials, often referred to as raschig rings.
These rings increase the contact surface area between the gas and the liquid, allowing for maximum interaction. As the gas ascends through the scrubber, it encounters a downward flow of liquid. The liquid phase absorbs the pollutants from the gas, effectively neutralizing harmful components such as acids or particulate matter. The cleaned gas then exits the scrubber, while the liquid phase, now containing absorbed pollutants, is collected for further treatment.
Chemical Reactions and Corrosivity
During the scrubbing process, the liquid phase can become acidic due to the absorption of pollutants like sulfur dioxide (SO₂) and nitrogen oxides (NOₓ). These acids, combined with high temperatures and chemical concentrations, create a highly corrosive environment within the scrubber. To mitigate this, the pH level of the liquid phase is continuously monitored and adjusted, often by adding neutralizing agents to maintain a basic or neutral pH level.
System Design Considerations
The efficiency of a scrubber system depends on several factors, including:
- Gas Velocity: The speed at which the gas moves through the scrubber affects the contact time between the gas and the liquid. Higher velocities may reduce the efficiency of pollutant removal.
- Filtering Length: The length of the scrubber and the volume of packing materials play a crucial role in determining the system's efficiency.
- Liquid Flow Rate: The rate at which the liquid is circulated through the system affects its ability to absorb pollutants. A balance must be maintained to ensure optimal performance.
The exhaust fan must be properly sized to handle the flow of waste gases and overcome the internal pressure of the scrubber. The design should also consider ease of maintenance, low operating costs, and minimal water consumption.
Material Selection
Given the corrosive nature of the absorbed pollutants, scrubber components are typically made from materials with high chemical resistance. Polypropylene (PP) and polyethylene (PE) are commonly used due to their ability to withstand long-term exposure to acids and other corrosive substances.
Wet Scrubber Systems
Wet scrubbers are a specific type of gas washing system that uses a liquid—often water or a water-based solution—to remove pollutants from industrial exhaust gases (also known as flue gas). Wet scrubbers are particularly effective at removing acidic gases like sulfur dioxide, which contribute to environmental issues such as acid rain.
Operation of Wet Scrubbers
In a wet scrubber system, the flue gas is directed through a chamber where it is sprayed with the scrubbing liquid. Water is the most common scrubbing medium, especially when dust and particulate matter are the primary pollutants. However, various chemicals can be added to the water to target specific contaminants. For example, alkaline solutions like lime or sodium hydroxide are often used to neutralize acidic gases.
As the gas passes through the scrubbing liquid, pollutants are absorbed or chemically reacted within the liquid phase. The heavier particles and contaminants are removed from the gas stream and settle in the liquid. The cleaned gas, now free of harmful pollutants, exits the scrubber and is released into the atmosphere.
Variations in Wet Scrubber Design
There are several design variations for wet scrubbers:
- Spray Tower Scrubbers: These are the most common type of wet scrubbers, where the gas is sprayed with a fine mist of the scrubbing liquid. The mist increases the contact area, allowing for efficient pollutant removal.
- Venturi Scrubbers: These systems accelerate the gas flow through a narrow passage, where it collides with the scrubbing liquid at high speeds. The intense mixing leads to high-efficiency particulate removal.
- Packed Bed Scrubbers: These use packing materials (such as raschig rings) to increase the surface area for gas-liquid contact. The gas flows through the packing material, where it interacts with the scrubbing liquid.
- Bubbling Scrubbers: In this design, the gas is forced to bubble through a pool of scrubbing liquid. This method provides effective removal of soluble gases but is less efficient for particulate matter.
Environmental Impact and Waste Management
The use of wet scrubbers significantly reduces the emission of harmful pollutants into the atmosphere, improving air quality and reducing environmental health risks. However, the scrubbing process generates waste in the form of spent scrubbing liquid, which contains absorbed pollutants. This liquid cannot be disposed of directly due to its hazardous nature and must be treated or neutralized before disposal.
The environmental benefits of wet scrubbing are substantial, but they come with the challenge of managing the waste products. Innovations in waste treatment and recycling are crucial for minimizing the environmental footprint of wet scrubbing systems.
Chemical gas washing systems (scrubbers) are essential for controlling industrial emissions and protecting the environment. These systems, whether wet or dry, operate on the principle of gas absorption in liquids, effectively removing pollutants from exhaust gases. Proper design, material selection, and system maintenance are critical for ensuring the efficiency and longevity of scrubbers.
Wet scrubbers, in particular, are widely used in industries that generate acidic gases and particulate matter. Despite the challenges of waste management, the environmental benefits of using scrubbers are undeniable, making them a vital component of industrial air pollution control strategies.
For more information visit: https://ergil.com/scrubber-systems/