Flame Arrestors & Storage Tank Valves
Crucial Part of Your Pipeline Operation Integrity; Safe, Reliable and Sustainable
Storagetech is an Atex certified designer and manufacturer with extensive experience providing technologically advanced atmospheric storage tank and pipeline safety breather valves, vents and flame arrestors for oil, gas, biogas, petrochemical, chemical, pharmaceutical, agro, water, wastewater treatment, and utility industries.
According to the academic resources, the operating principle of Flame Arrestor was founded in 1815, England at the Royal Institution of England. A committee of the English coal mining industry had needed for a protection method to prevent miners 'oil lamps from causing explosions when flammable gas called firedamp seeped into the mine shafts.
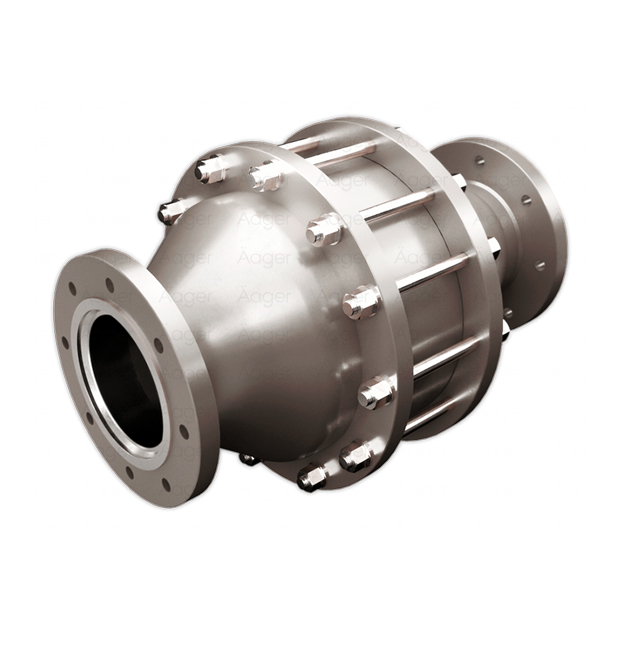
Flame and detonation arrester, although similar in construction, serve two very distinct purposes. Here answer some of the most common questions asked about flame and detonation arresters.
A flame arrester is a safety device that is used on the pipeline or end of the line to block any fire or explosion passage through the line. There are mainly two types of flame arrester; detonation and deflagration.
Detonation flame arrester is designed to overcome any sudden explosion impact in the pipeline, whereas deflagration is flame arrester is designed to block any fire flame in a particular location to stop fire to travel in the pipeline freely.
Storagetech technical team is experienced to choose which type of flame arrester is required for a particular application. Even though there are many factors to choose, mainly location, product stored, and pipeline/piping design plays an important role.
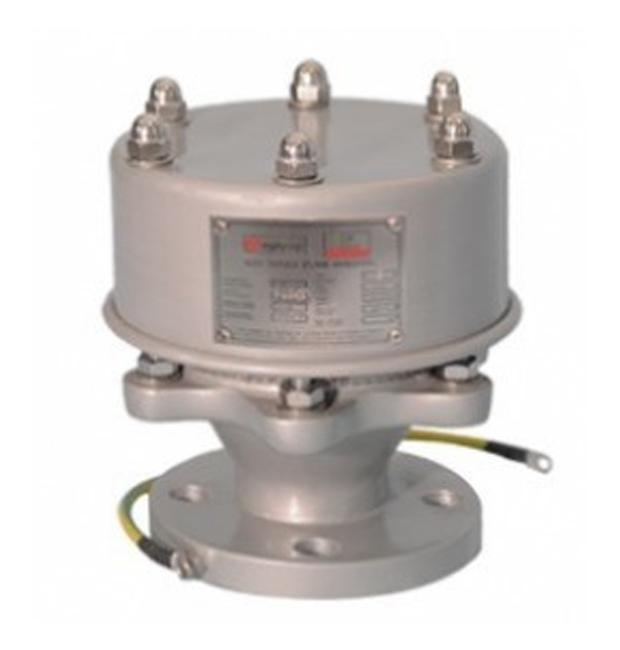
End-of-line Flame Arrestors
This type of flame arrester is installed on low-pressure storage processing tanks, bleed tanks, or other waste gas devices. Normally, they are installed on a vent nozzle mounted on a tank that is discharged directly into the atmosphere. They can also be incorporated as integral parts of conservation vents installed on atmospheric storage tanks containing flammable liquids. It should be noted that flame arresters are not always necessary as part of conservation vents.
The gases produced by vaporization of many flammable liquids have similar flame speeds when mixed with air. Typical of these are gasoline, jet fuel, benzene, plastics monomers, and organic solvents. Often the pressure drop across the vent valve of a conservation vent is a ¾ inch (17mm) of water or more. In this case, the velocity of the gas flow through the vent-valve opening will be higher than the speed at which the flame can propagate upstream through the opening.
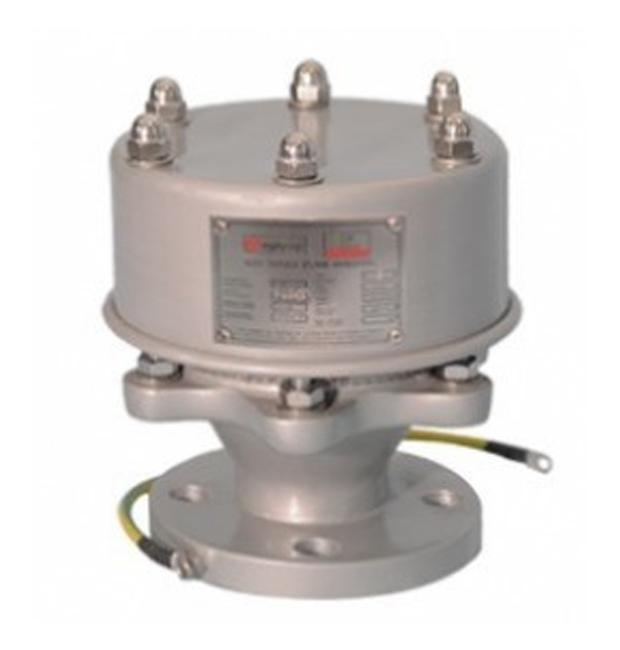
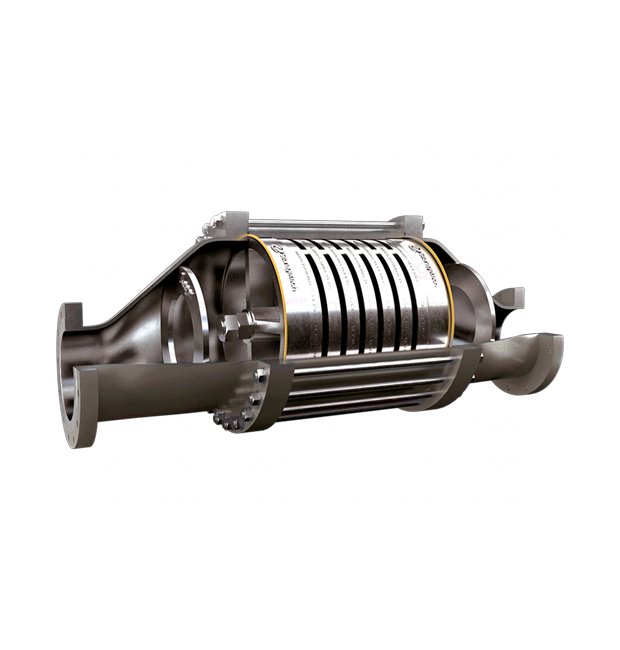
In-line Flame Arrestors
Sometimes it is desirable to install flame arresters in the middle of a long pipeline. They are particularly suited for installation inside a tank house where vent pipes or lines are extended through the tank house roof or walls to the outside. Locating the unit inside eliminates difficult inspections on the storage tank roof and protects the vent from the freezing of condensate.
Combustion in a pipeline can readily make the transition from deflagration than detonation; in the case of some designs, a detonation can be stopped, whereas a deflagration may pass through. Therefore, an in-line flame arrester must withstand and stop both types of combustion from both downstream and upstream in a pipeline.
Since the pressures developed in the combustion can be high, the in-line arrester and pipeline must be properly designed, constructed and tested. The flame arrester element itself must be capable of withstanding substantial pressure differentials in both directions as a result of the combustion.
STORAGE TANK VALVES
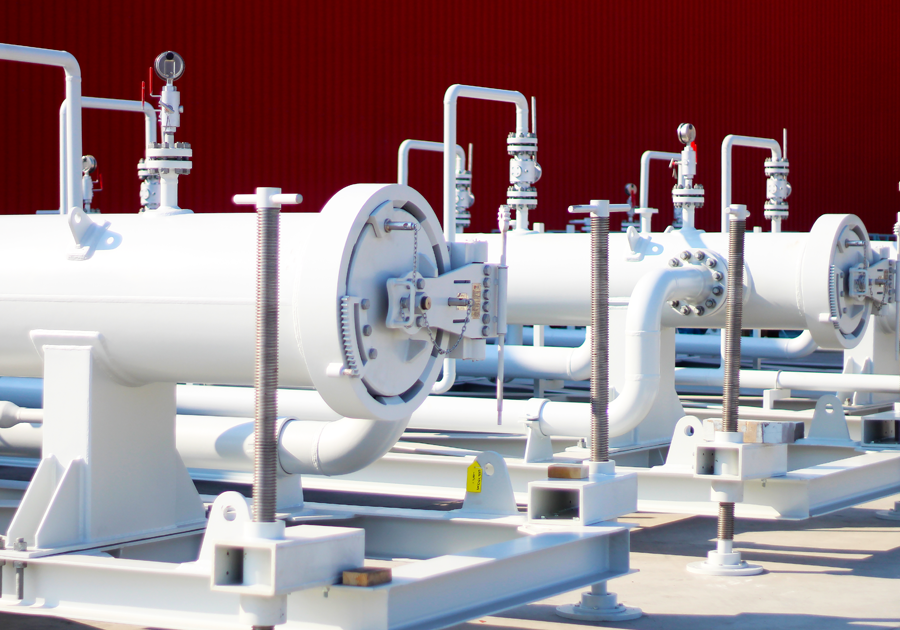
Deflagration Flame Arrestors
A flame arrester, designed to perform as an extinguishing barrier, which absorbs and dispels heat, reduces fire temperature and the oxygen level to stop the fire through layers of metal ribbons shaped with crimped corrugations. It is mounted either vertically or horizontally (some cases) between two lines or used with the pressure-vacuum vent on storage tanks.
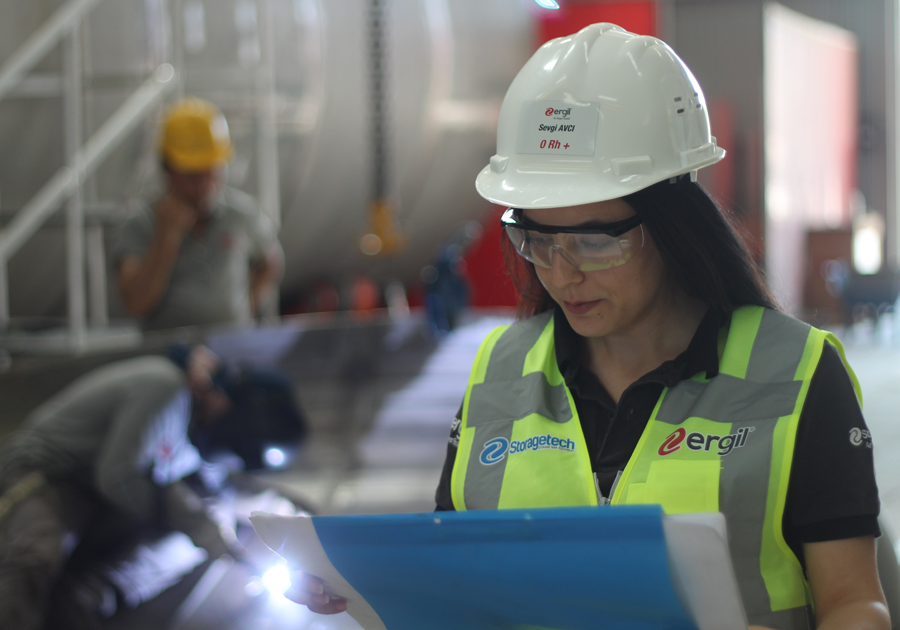
Detonation Flame Arrestors
A flame arrester, intended to withstand higher pressures and continuous a flame than the deflagration flame arresters. Detonation Flame Arrester is designed for installation in gas pipelines. Detonation occurs when a flame travelling through the pipeline reaches supersonic velocities, usually as a result of the pipeline configuration or pipeline surface roughness. Changes in gas density and pressure produce the flame velocity to metamorphose from subsonic to supersonic. The flame quenching element is designed to be three or four times the area of the pipe in which it is installed, and is assembled between two flanged reducing spools.
The element comprises a tightly rolled scroll or scrolls of crimped stainless steel ribbon to form passages through which the vapour passes. The area of each passage determines the level of protection that the element provides. It has a maximum experimental safe gap (MESG) as per the model and is suitable for gas groups IIB and IIA. The detonation flame arrestor is more robust than the deflagration flame arrester, and contiguous scrolls have smaller MESGs to withstand higher pressures and to quench detonations.
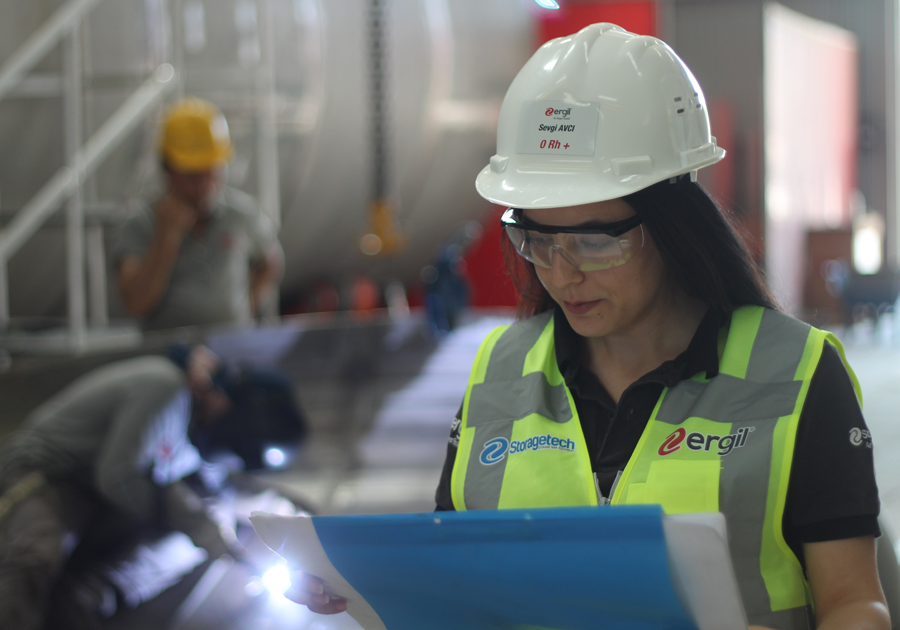
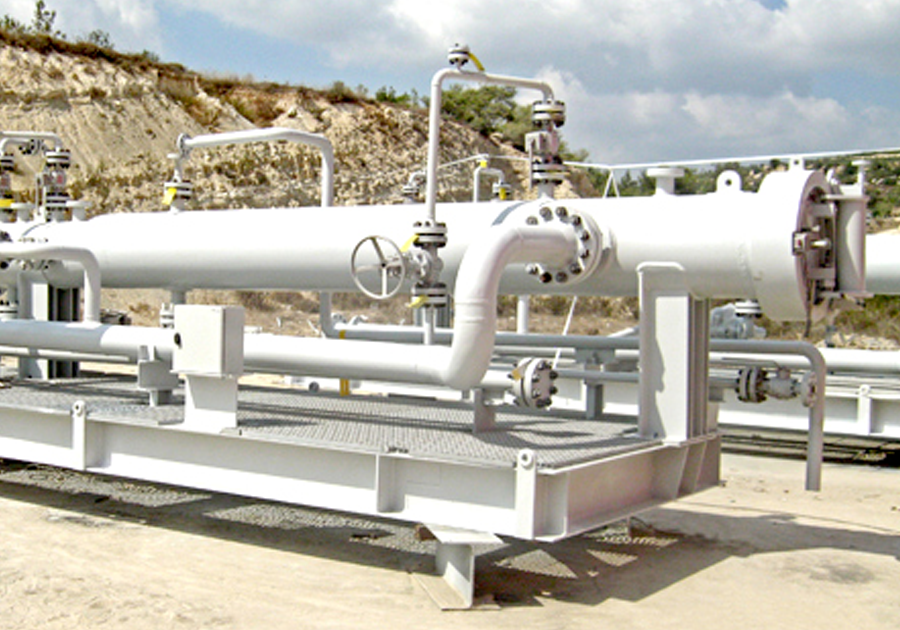
Storage Tank Pressure Relief Valve
A Storage Tank Pressure Vacuum Relief Valve is a safety device designed to protect storage tanks or pressure vessels by releasing pressure directly to the atmosphere. The Pressure vacuum vent protects the storage tanks against excessive pressure or vacuum generated in the tank. The vent performs as an inhaler under pressure or as a discharger of overpressure.
When air pressure exceeds the preset setting of pressure vacuum vent, the pallet opens, departs the seal, and expels any excessive negative or positive pressure. They are commonly mounted to a flange or pipe, which connects the vapor space of a storage tank.
Dependent upon specific requirements, the vents can be applied to desired specifications allowing the pallet assemblies to open when specific pressure and vacuum levels are reached.
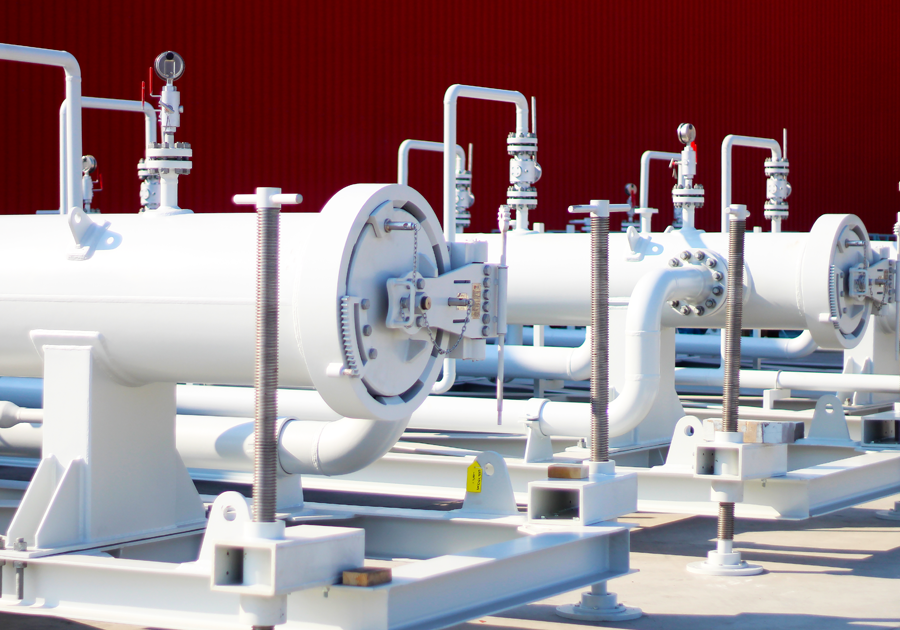
Emergency Relief Valve
An Emergency Pressure Relief Valve operates in the last resort when a vessel or storage tank is exposed to a large-scale fire, and the standard pressure relief valve has failed to open or cope with the extreme conditions.
Designed to open in the event of high pressure, the set-pressure should be chosen to be above that of the pressure or pressure-vacuum relief valve. When the set pressure is reached, the vent cover rises sufficiently to dissipate the pressure in the tank.
The weight-loaded emergency pressure relief vent is installed in the horizontal plane on a flange at the top of the tank. A secondary use of the unit is to access the tank for product sampling or depth gauging.
Request A Quote
Do you need a quick quotation? Fill out the below form and expect our reply soon
Projects
Discover Our Global Success Stories: Join the Journey of Inspiration!
News, Events & Case Studies
Dive into a World of Knowledge and Insight: Explore Our News, Events, Articles, and Case Studies!
Pipeline Pigging System FAQ's
Find Out More About Us
Our people are our biggest asset but the only way to unlock their potential is to invest in the right business systems that encourage innovation.
More than 40 years of experience
Easily Reachable
Worldwide Offices and Representatives
Superior After Sales Support
Long-term business partnerships
Certifications ATEX, ASME, ISO, CE
High-end Production Facility
35,000 square meter manufacturing facility
Being leader in manufacturing better, safer, and economical products
Contribute positively to our communities and environments well as to ensure highest level of customer satisfaction through the highest standards of excellence in our products and services, and comprehensive environmental regulations. Working everyday for the creation of better products that protects environment, people and assets.
Our history begins in 1938 and goes on together with all our parties.
- 1983 - Founded
- 1987 - Added 100. product to its portfolio
- 1991 - Certified products and services
- 2005 - Opened its first international office
- 2010 - Became market leader in 11 countries
- 2010 - Invested heavily in new manufacturing facility
- 2015 - Build one of the biggest R&D in its-field
- 2018 - Became part of Äager